This job description outlines the essential functions of the role; however, it does not limit or dictate the specific tasks that may be assigned. This is an On-Site position requiring full-time work at the plant. We strongly encourage veterans, minorities, and women to apply.
SUMMARY:
The production supervisor is responsible for assuring compliance with occupational health, safety, environmental, food quality and personnel policy compliance. Has overall responsibility for planning, organizing, directing, and coordinating the production teams in processing or packaging and assigning associates to positions. Supports team objectives by providing adequate resources and materials necessary to work safely and maintain a high level of production efficiency within the annual budget plan. Provides leadership through example, motivates individuals, builds team spirit and counsels associates to achieve excellence. Supports implementation and development of continuous improvement through coaching, mentoring and annual objectives.
ESSENTIAL DUTIES AND RESPONSIBILITIES:
- Perform all duties and responsibilities in accordance with Mizkan America safety policies, OSHA regulations, GMP (Good Manufacturing Practices), and SOP (Standard Operating Procedures).
- Provide adequate staff levels on teams to meet production plan requirements.
- Coordinates activities of teams to maximize labor effectiveness and assure adequate breaks.
- Observes teams and ensures compliance with safety, health and environmental rules and guidelines. Corrects unsafe acts and conditions.
- Completes daily reports.
- Lead teams in weekly scheduled meetings.
- Work cross functionally with all facility teams to improve line efficiencies, RCA etc.
- Provides leadership and ensures full completion of assigned line improvement projects.
- Leads team to maximize yields and minimize waste.
- Order and approve supply needs for the team/area.
- Stays up to date on all equipment and processes in the area.
- Is able to improve and develop team members’ performance through effective coaching and ensure compliance with policy guidelines for corrective steps.
- Monitors completion of preventative inspections and restorative work in effort to support reliable operation of equipment in area.
- Teaches/coaches production operators and maintenance associates through process of implementing principles of Continuous Improvement.
- Able to coach, teach, learn and run processing equipment, to eliminate overtime and shutting down for breaks when needed.
EDUCATION:
- High school diploma or G.E.D. equivalent required.
- Bachelor’s degree
EXPERIENCE AND QUALIFICATIONS:
- A minimum of 3-5 year’s experience of leadership in a manufacturing environment.
- Excellent communication skills
- Familiar with HACCAP
- Familiar with D365
- Good interpersonal skills with the ability to collaborate effectively with individuals and groups at all levels of the organization.
- Strong organizational, problem-solving, and analytical skills.
- Strong Computer Literacy skills.
- Willingness and flexibility to adapt to changing business needs and deadlines.
- Ability to exhibit a professional business-like appearance and demeanor. · Must be able to multitask and prioritize job duties.
- Be able to articulate through written communication.
- Willing to challenge or counsel individuals according to company policies.
- Capable of open communication in order to LISTEN to other opinions, to obtain best results for production goals.
- Ability to work in elevated temperatures (hot or cold), working at heights and exposure to strong smells, dust, gases, fumes and chemical or require personal protective equipment.
- Ability to use Personal Protective Equipment.
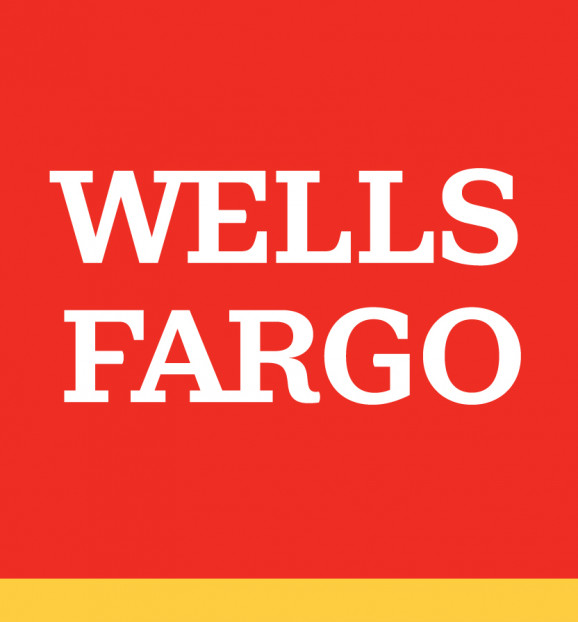
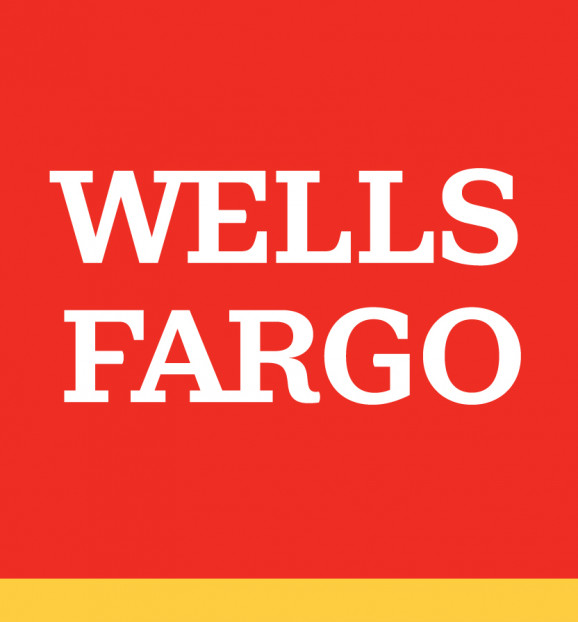
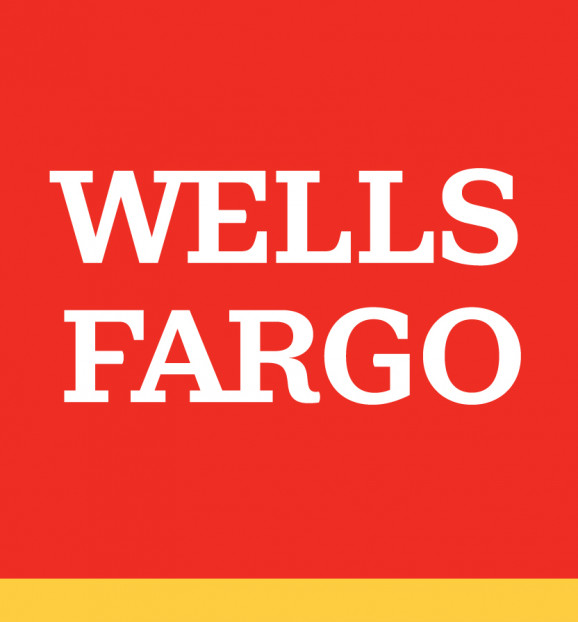