Full Job Description
Location: Lake Alfred
Job Title: PLANT MANAGER
Department: Operations
Reports To: Regional Director of Bottling Operations
FLSA Status: Exempt
Back Up: Production Manager / Bottling Manager / Bulk Manager
COMMENTS: This job description reflects assignment of essential functions, it does not prescribe or restrict the tasks that may be assigned.
SUMMARY: The Plant Manager will be responsible for the overall operations of the bottling plant in which they are assigned. They are the senior site manager for their location.
ESSENTIAL DUTIES AND RESPONSIBILITIES include the following. Other duties may be assigned.
• Direct the day-to-day operations of the facility through department managers and support staff.
• Analyze manufacturing, personnel, materials, logistics, and other problems. Champion high priority corrective actions.
• Build a strong, achievement-oriented team by using the appropriate mix of hiring, delegation, training, monitoring, feedback, coaching, motivation, mentoring, and employee retention techniques.
• Ensure plant staff enforces company policies and procedures, plant-wide safety and security rules, and employee rules of conduct.
• Integrate organizational changes and new processes.
• Ensure customer satisfaction through corrective and preventive actions and the application of continuous product quality improvements.
• Ensure plant sanitation and quality standards are consistent with federal, state, local, and company requirements.
• Interface with AIB, Kosher Council, State/Federal agencies (FDA, OSHA, EPA, etc.), third party auditors, and other regulatory agencies. Address issues pertaining to product quality, wastewater treatment, air quality, etc.
• Recommend the plant’s operating budget. Manage and control expenditures and variances.
• Manage assets and ensure inventory accuracy.
• Reduce scrap and waste and initiate other cost reduction activities throughout the facility.
• Identify, research, propose, implement, track, and evaluate capital projects.
• Provide timely information and reports on issues that affect plant performance and other critical matters.
• Oversee the development, implementation, and adherence of SOP’s that result in improved product quality and efficiency levels.
• Achieve and maintain 98% perfect order completion and delivery.
• Promote operational excellence throughout the plant.
• Respond to emergency calls as required
• Responsible for Food Quality, Safety and Legality.
EDUCATION, EXPERIENCE AND QUALIFICATIONS:
• Bachelor Degree preferred.
• 10 years management experience in manufacturing.
• 3 - 5 years experience in Plant Manager or equivalent role.
• Should have experience working in liquid fill or other consumer packaging.
• Must posses the ability to work with all levels of employees in the organization.
• Solid understanding of Supply Chain Management, Procurement, Maintenance, Transportation, Packaging and Safety,
• Must be well organized, results oriented, & have effective problem solving ability
• Must possess strong leadership & team building skills
• Must be computer literate – Microsoft Office Programs & AS 400 is desirable
• Good organizational skills
• Show good judgment and sound reasoning skills
• Ability to delegate authority
• Must have a strong floor presence and be able to interact effectively with people at all levels.
• Ability to lift and move over 50 pounds with or without reasonable accommodation is required.
Equal Opportunity Employer Minorities/Women/Protected Veterans/Disabled
Job Title: PLANT MANAGER
Department: Operations
Reports To: Regional Director of Bottling Operations
FLSA Status: Exempt
Back Up: Production Manager / Bottling Manager / Bulk Manager
COMMENTS: This job description reflects assignment of essential functions, it does not prescribe or restrict the tasks that may be assigned.
SUMMARY: The Plant Manager will be responsible for the overall operations of the bottling plant in which they are assigned. They are the senior site manager for their location.
ESSENTIAL DUTIES AND RESPONSIBILITIES include the following. Other duties may be assigned.
• Direct the day-to-day operations of the facility through department managers and support staff.
• Analyze manufacturing, personnel, materials, logistics, and other problems. Champion high priority corrective actions.
• Build a strong, achievement-oriented team by using the appropriate mix of hiring, delegation, training, monitoring, feedback, coaching, motivation, mentoring, and employee retention techniques.
• Ensure plant staff enforces company policies and procedures, plant-wide safety and security rules, and employee rules of conduct.
• Integrate organizational changes and new processes.
• Ensure customer satisfaction through corrective and preventive actions and the application of continuous product quality improvements.
• Ensure plant sanitation and quality standards are consistent with federal, state, local, and company requirements.
• Interface with AIB, Kosher Council, State/Federal agencies (FDA, OSHA, EPA, etc.), third party auditors, and other regulatory agencies. Address issues pertaining to product quality, wastewater treatment, air quality, etc.
• Recommend the plant’s operating budget. Manage and control expenditures and variances.
• Manage assets and ensure inventory accuracy.
• Reduce scrap and waste and initiate other cost reduction activities throughout the facility.
• Identify, research, propose, implement, track, and evaluate capital projects.
• Provide timely information and reports on issues that affect plant performance and other critical matters.
• Oversee the development, implementation, and adherence of SOP’s that result in improved product quality and efficiency levels.
• Achieve and maintain 98% perfect order completion and delivery.
• Promote operational excellence throughout the plant.
• Respond to emergency calls as required
• Responsible for Food Quality, Safety and Legality.
EDUCATION, EXPERIENCE AND QUALIFICATIONS:
• Bachelor Degree preferred.
• 10 years management experience in manufacturing.
• 3 - 5 years experience in Plant Manager or equivalent role.
• Should have experience working in liquid fill or other consumer packaging.
• Must posses the ability to work with all levels of employees in the organization.
• Solid understanding of Supply Chain Management, Procurement, Maintenance, Transportation, Packaging and Safety,
• Must be well organized, results oriented, & have effective problem solving ability
• Must possess strong leadership & team building skills
• Must be computer literate – Microsoft Office Programs & AS 400 is desirable
• Good organizational skills
• Show good judgment and sound reasoning skills
• Ability to delegate authority
• Must have a strong floor presence and be able to interact effectively with people at all levels.
• Ability to lift and move over 50 pounds with or without reasonable accommodation is required.
Equal Opportunity Employer Minorities/Women/Protected Veterans/Disabled
Job Information
Job Category:
Manufacturing
Spotlight
Employer
Related jobs
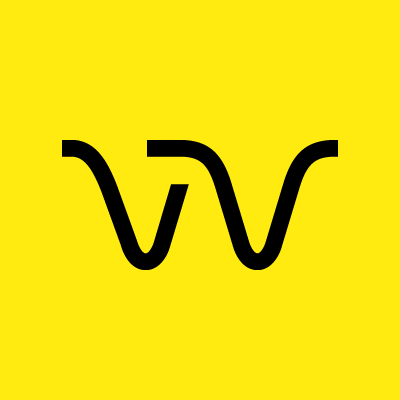
The primary responsibility of this position is leading a site Procurement team, building and executing partnering with our global operations and business leaders to providing strategic sourcing expe...
Mar 6, 2025
Hopkinton, MA
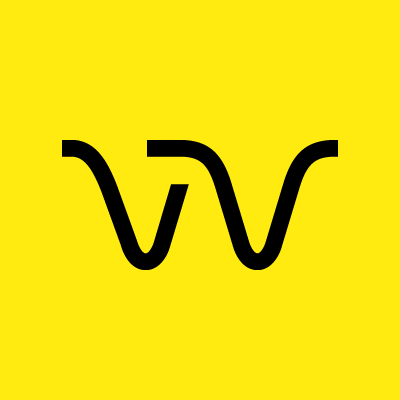
Sales Specialist, LabChip
Revvity
The Sales Specialist, LabChip is responsible for Direct Sales of the LabChip GX and GXII Touch Microfluidics Platforms and Consumables primarily in the Mid-Atlantic. This includes: Management of key...
Mar 6, 2025
PA
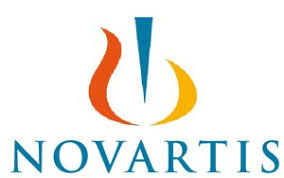
Job Description SummaryThis is a field-based and remote opportunity supporting key accounts in an assigned geography.Novartis is unable to offer relocation support for this role. Please only apply if...
Mar 6, 2025